1. Real-Time Process Control & Automation
IPCs act as the central brain of smart factories, processing data from IoT sensors, CNC machines, and robotic arms. By running SCADA systems and edge computing algorithms, they enable:
- Precise control of production lines.
- Instant adjustments to minimize waste (e.g., material usage, energy).
- Automated quality checks via AI-powered vision systems.
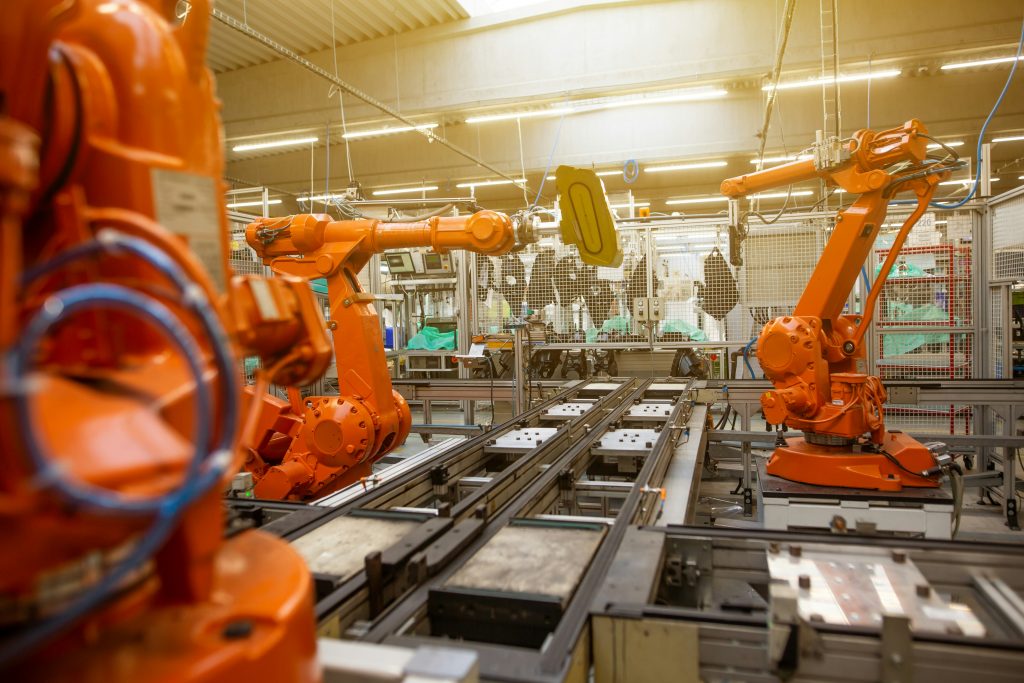
2. Predictive Maintenance & Downtime Prevention
Unplanned downtime costs manufacturers $50 billion annually. IPCs combat this by:
- Monitoring equipment health (vibration, temperature, power draw).
- Flagging anomalies using machine learning.
- Triggering maintenance alerts before failures occur.
3. Energy Optimization & Sustainability
Smart factories leverage IPCs to slash energy costs by:
- Dynamically adjusting HVAC and lighting based on occupancy.
- Optimizing motor speeds to match production demands.
- Tracking carbon footprints for compliance reporting.
4. Secure Data Management & Edge Computing
IPCs process data locally, minimizing latency and cloud dependency. With cybersecurity features like TPM 2.0 and VLAN support, they:
- Protect sensitive production data from breaches.
- Enable real-time analytics for faster decision-making.
- Integrate with MES/ERP systems for end-to-end visibility.
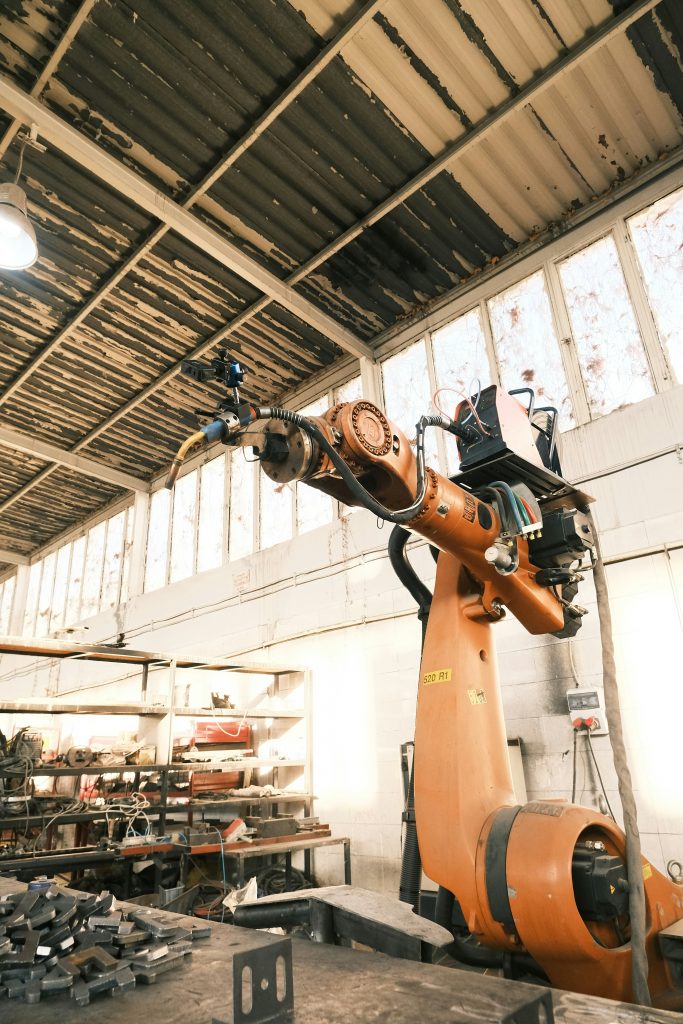
5. Scalable IIoT Integration
From legacy machines to 5G-enabled robots, IPCs bridge the gap between old and new. Their modular design supports:
- Retrofit upgrades for older facilities.
- Plug-and-play connectivity with OPC UA, Modbus, and MQTT protocols.
- Centralized monitoring via customizable HMIs.
Choosing the Right IPC: 3 Factors for Success
Not all IPCs are created equal. Prioritize these features for maximum ROI:
- Ruggedness: Look for IP65/IP67 ratings and wide temperature tolerance.
- Expandability: Ensure support for future I/O expansions (e.g., PoE+, PCIe slots).
- Software Compatibility: Opt for Windows/Linux-based systems with Docker/container support.